Home | Op Editorials | Swimming Pool Expert Witness - Paolo Benedetti | Utilizing Drainage Mats In Pool Construction
Retaining walls, raised pool bond beams and pools with adjacent upslopes all require drainage behind them. But it is impossible to install drainage rock up the walls of a shotcrete pool, without extensive over-excavation, forming and backfilling. Pvc Dense Groove Drainage Board
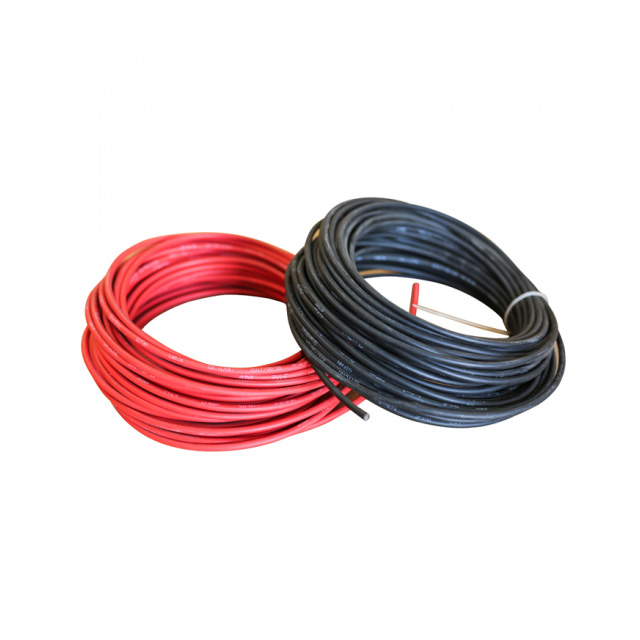
Instead of ignoring these conditions, wise contractors utilize drainage mats installed upon the earth, prior to the placement of the shotcrete. This allows the subterranean water to drain vertically into the drain rock under the pool, where it can be collected and discharged (drained to daylight or via a sump pump).
For high-end projects or all tile vessels, this is critical in reducing negative side water infiltration from the soils. Water passes through the geofabric and into the air gap created by the dimples in the plastic sheet. The drainage mats are available with dimples of various sizes to match the anticipated water flow.
Drainage mats can also be used horizontally between coffers and vessels to assist in the lateral discharge of water. The drainage mats can be nailed to the soil prior to steel placement or utilized in place of steel-tex.
Photo Credits: Carlisle Coatings & Waterproofing Systems
Hair Entanglement in Pools, Are Current Standards Adequate?
Indoor Pools & Water Vapor, What You Need To Know
Paolo Benedetti is the President of Aquatic Technology and better known on social media as the "Swimming Pool Expert Witness". Paolo is an instructor at Watershape University and has authored a myriad of articles on the finer points of pool construction and design. He is a pioneer in the field of aquatic design, constantly pushing the envelope, creating a number of firsts that spawned new trends in the industry.
Keith Zars – One on One with Pool Magazine
What Do You Do If Your Pool Builder Abandons The Project?
Pool Techs Cash In On Hayward’s “Get Paid To Upgrade” Program
Banned For Life – Olympus Pools Owner Agrees To AG Settlement
Setting The Standard – Paolo Benedetti
Movable Floors Are Taking Flexibility Of Indoor And Outdoor Living To A Whole New Level
Before you choose a pool tile, read this informative article.
Pool industry professionals certainly came away excited about all of the new and innovative products and materials they saw at the recent Coverings event in Orlando, Fl. However, when selecting which pool tile materials to use it is vital to learn the differences between the US ANSI standards and the EU ISO standards which are not the same. Consequently, ANSI standards are more stringent.
It’s important not to buy into the sales presentation and perform your due diligence before choosing a product. Using materials that are not suitable for the application could potentially expose you to liability should there be a failure.
ANSI A137-2017 are the standards for tile performance (A137.1 Ceramic Tiles & A137.2 Glass Tiles). Below are the minimum performance characteristics for ceramic tiles for submerged aquatic applications, the applicable test methods, and the minimum standards required.
One important factor to consider, porcelain tiles are 50% feldspar and are fired at much higher temperatures than regular ceramic tiles. This makes them much harder and denser than regular ceramic tiles. Porcelain tiles are a sub-group of the broader ceramic tile group, to which these standards apply.
There are two types: Static (SCOF) and Dynamic (DCOF). COF is the ratio of forces necessary to initiate sliding between two surfaces. The outdated ASTM C1028 static test measured the SCOF.
DCOF is the ratio of the force necessary to maintain sliding between two surfaces. The higher the DCOF, the more slip resistant the surface. This may not be of any concern underwater, but of grave concern on a pool deck or locker room floor. Industry standards generally accept ≥0.42 DCOF for commercial floor applications. Wet/dry locations, like aquatic locker rooms or moveable pool floors, may require ≥0.60 DCOF.
Tiles are weighed dry and again after soaking in water. The weight gain determines the percentage of absorption. Tiles are rated as follows:
Impervious: Tiles exhibiting 0.5% or less.
Vitreous: Tiles exhibiting more than 0.5%, but not more than 3.0%.
Semi-Vitreous: Tiles exhibiting more than 3.0%, but not more than 7.0%.
Non-Vitreous: Tiles exhibiting more than 7.0%.
Directly related to water absorption. You can see that any absorbed water will be detrimental in a freeze condition – the expansion of freezing water will crack the tiles. Porcelain tile, by definition has a water absorption of less than 0.5%, making it frost proof as well. For aquatic applications we want impervious pool tile materials.
The hardness of a tile’s surface will determine how it wears. The surface is scratched and a MOH’s hardness rating assigned. MOH’s scale 1- Talc (softest) to 10 Diamond (hardest). A hardness of 5 is suitable for residential flooring. A hardness of 7 or greater is usually recommended for commercial or outdoor applications.
Ceramic floor tiles must be able to support the loads exerted upon them. The test applies a force in pounds, to an unsupported tile until it breaks. Your selection should be based upon the anticipated maximum loads. Properly installed tiles, with a supporting setting bed that is free of voids, will be able to support significantly greater loads. These breaking values are for comparison purposes.
In this test, sample tiles are placed in various chemical baths for 24 hours, rinsed and examined for surface damage. For aquatic venues, it is desired to have the greatest level of chemical resistance.
This is a purely a cosmetic evaluation as to the consistency of the tile shades within a production lot.
Monochromatic (V0) – Very uniform, monochromatic color.
Low (V1) – Consistent color within each tile and from tile to tile.
Medium (V2) – Color variation within each tile.
High (V3) – Variation from tile to tile & within each tile.
Random (V4) – Considerable variation from tile to tile.
The durability of the glazed surface is examined following the abrasion testing. The performance classifications and recommended uses are listed below:
CLASS 0 – Not recommended for use on floors.
CLASS 1 – (Light Residential) Light Traffic – Residential floor coverings in areas subject to soft-soled footwear or normal footwear traffic, without scratching dirt (i.e. domestic bathrooms and bedrooms without exterior access).
CLASS 2 (Residential) Medium to Light Traffic – Residential floor coverings in areas subject to soft-soled footwear or normal footwear traffic with small amounts of scratching dirt (i.e. rooms in the living areas of homes except kitchens, entrances and other areas that may be subjected to high usage).
CLASS 3 (Heavy Residential or Light Commercial) Medium to Heavy Traffic – Residential or light commercial may withstand normal footwear and regular traffic, with some dirt and/or other abrasives present in limited quantities. Tile in this class may be used in light commercial installations with limited foot traffic and with no direct access to the outside. Examples may include residential kitchens and hallways with limited traffic from the outside.
CLASS 4 (Commercial) Heavy Traffic – Residential and commercial floor coverings subjected to considerable traffic and scratching dirt (i.e. entrances, workrooms, inns, exhibition halls, and sales rooms, as well as other rooms in public and private buildings). Floors should be adequately protected against scratching dirt at the entrances to buildings by either floor mats or some other footwear cleaning device.
CLASS 5 (Heavy Commercial) Heavy Traffic – Heavy commercial floor coverings subject to heavy traffic with very abrasive soil.
This test is intended to determine the resistance to staining of tile surfaces. Class A – provides maximum stain resistance
While not a part of the ANSI A137.1 standard, in submerged applications, the TCNA standards require that 95% of the back of the tile be in contact with the thinset. Care must be taken when choosing a porcelain tile for an aquatic environment, to ensure that the combination of the mesh and glue to not occupy more than 5% of the contact surface. It’s easy to evaluate the mesh, but not the glue. Worse yet, is if the glues soften in water.
To summarize when selecting the best pool tile materials for aquatic applications we would desire the following minimum characteristics:
1. DCOF – not critical in submerged applications, but values of ≥0.42 for flooring, ≥0.60 wet/dry floors.
2. Water Absorption – Impervious, Tiles exhibiting 0.5% or less.
4. SCRATCH HARDNESS – MOH’s 6-7.
5. BREAKING STRENGTH – Exceed PSI loads.
10. MOUNTING METHOD – free of glue and mesh backing.
Below are the equivalent US / ISO European standards:
A pool builder experimenting with movable pool floors was a costly lesson. Learn how this moving pool floor project was saved.
It started with a phone call from the owner’s personal assistant. They had movable pool floors in the pool and spa that didn’t operate properly. They wondered if I’d fly up to Whitefish, MT, and have a look-see at their problems.
Upon my arrival, I was met with an odd home-brew moving floor system. In an attempt to reinvent the wheel, the pool builder attempted to create his own moving floor systems. The premise was that ballast tanks would be filled with water to lower the floor and be filled with air to raise it.
In theory, it may have worked, but as with any unproved and untested design, there are always kinks. Testing theories on a wealthy client and working out the kinks on a multi-million dollar pool project, is never the place to learn.
To begin with, the structure was fabricated out of aluminum. Anyone who’s spent time around chlorinated swimming pools knows that aluminum rapidly decays in salt or chlorinated water. The ballast tanks did not have any bulkheads, so the water sloshed from end to end. This caused the floor to list to one side or end, binding it within the pool walls. You can imagine a multi-ton structure wedged within the pool walls. The deck of the floors were finished in Ipe, a hard exotic hardwood. However, after submersion in water, the wood becomes gray, slimy, and slippery.
To make matters worse, the builder failed to recess the incandescent lights and wall fittings. So the shifting floor structure would sheer off the glass lenses and fittings. In a futile attempt to keep the multi-ton structure aligned, the builder cut guide tracks into the walls and installed roller wheels. Again, the forces at play here grossly exceeded the bolt-on wheel assemblies.
The moving floor in the spa was another disaster. The mechanism was a scissors lift, driven by a hydraulic ram. The builder sourced his hydraulic ram from a local tractor supply store. Over a few quick months, the leaking ram created an oil slick atop the spa. Needless to say, the cast iron ram began to corrode within the chlorinated water.
Once I began to evaluate the hydraulics, electrical, and moving floor systems, it became apparent that the entire project would require a substantial renovation in order to be safe, functional, and code compliant.
I partnered with a local contractor, Shawn Hossack of Panorama Builders. Together we came up with a plan to remove the dangerous floor system and install a new fully proven and engineered system. Though we obtained bids from a number of manufacturers, we settled on systems from Hydrofloors – Twinscape Group. Their technical support and proven track record made the client’s choice simple.
The interior of the pool & spa was determined to be not completely plumb and true. The only means to correct these deviations would be to render them with mortar and tile them. First, the failing Eco-Finish would have to be removed from the walls, the walls roughened, and prepared for waterproofing.
Since winter was approaching, the decision was made to tent the project under a 100-foot by 50-foot tent and pump in 2,000,000 BTU of heated air 24/7. Over the winter months, the exterior temperature dropped to below -18ºF with the wind chill. Meanwhile, the interior temperature remained a comfortable 60ºF! The cost to operate the diesel heat exchanger and blowers averaged $10,000 a month.
To get the exact contours from which Twinscape could begin fabrication, the crews at Panorama tiled the top 3 feet of the pool in order to generate a 3-D model of the interior.
Since the walls are supposed to be perfectly vertical, these 3 feet would be a representation of the entire pool depth. From this model, Twinscape was able to begin fabrication, while progress was being made on tiling the pool.
The spa wasn’t quite deep enough to accommodate a properly designed scissors lift. We remedied this by raising the spa walls 18 inches and replumbing the jets. Once the concrete had cured, the tiling of the spa began in parallel with the pool.
The clients chose a beautiful blue tile from Interstyle. The hydraulics and mechanical systems were corrected to the best possible conditions without demolishing the decking and totally re-piping the pool and spa. Some pumps were eliminated and their pipes were re-purposed in order to reduce the line velocities on the remaining pumps. Some drains were converted to returns and unblockable drains and sump were installed. The ineffective skimmers in the catch basin were removed and their suction pipes were connected to the basin floor drains. Water chemistry management systems were installed to eliminate corrosion of the new floor systems.
During demolition, we discovered many electrical and bonding deficiencies. The incandescent lighting was converted to strip lights from Hydrolume and proper j-boxes and conduits were installed.
To eliminate the fall hazard over the vanishing edge, we partnered with Reynolds Polymers to fabricate and install an acrylic railing system. The panels were set into a channel within the floor. So, regardless of the height of the floor within the pool, there will always be a railing of sufficient height to protect pedestrians and bathers.
All in all, the repairs to the project took almost 20 months. The ensuing lawsuit resulted in a jury trial and a judgment of $4,750,000 – to date, the nation’s largest judgment in a residential pool construction defect case.
Avoid the negative spiral by adhering to 4 fundamental principles.
A lot of builders compete on price and operate on narrow margins. This leaves little revenue to perform warranty repairs or to correct errors made during construction.
These builders oftentimes rely on the profit from the next job to fix mistakes from the last project. As the economy slips into a recession, these revenues shrink even more and the pool of funds available to remediate mistakes dries up.
Delays in performing repairs increases and customer frustration grows. As customer complaints intensify, the quantity of lawsuits rise.
Now, more than ever, as the economy constricts, clients will become more frugal and conscience of what is occurring in their yard. They will be less tolerant of delays and excuses.
This was a post originally published on Facebook that received an enormous response from peers within the industry.
Thoughts from some of my followers:
I don’t play the race to the bottom game to get the job. I have my margins and if someone goes cheap, they can have the job. If I don’t make what I need to, I walk away.
Another way to remediate this is to ensure that your profit margins are adequate enough that you don’t have to rob Peter to pay Paul. If you’re actually performing quality work, the customer should be charged accordingly. Quality work costs money; most reasonable customers understand that.
Great advice. As a a 40+ year pool builder I wish just one of ex employees that decided to go into business for themselves would take the time to learn the business. I wouldn’t have made a career of repairing (and being paid well) for repairing others mistakes.
Recall on Aiper Elite Pro Cordless Robot Pool Vacuum Cleaners
Women Survive Maui Fire By Jumping in Swimming Pool
A New Era for Ledge Lounger : Chris Scherzinger Succeeds Founder Christopher Anderson
Pool Designers: Million Dollar Pool Challenge Now Accepting Entries
What Do You Do If Your Pool Builder Abandons The Project?
Florida Pool Owners Brace For Potential Category 3 Hurricane
Amazon Driver Beat The Heat By Diving Into Customer’s Pool
Spa Linked As Cause of Legionnaires’ Outbreak That Killed Two

Dimple Drainage Board Powered by © Copyright 2020-2023 - All Rights Reserved - Use of this site constitutes acceptance of our Privacy Policy Articles and content may not be reused without the expressed permission of Pool Magazine™.